トラロジでは、物流倉庫で利用される最新のロボットに大注目して独自に情報収集しています。今回は、ACRという物流ロボットについての特集です。保管・出荷の領域で高い生産性と保管効率を両立する、新しいタイプの物流ロボットとして期待の高いものです。
物流ロボットについて、その市場動向や代表的な種類、関連する情報システム、そして導入方法やその課題まで網羅した完全ガイドも合わせてご覧ください。
この記事では、物流ロボットとは何か、そしてその最新動向や課題をよく理解するための、特に重要な論点を幅広く取り上げます。 ・物流ロボットの市場動向 ・ロボットの主な種類と特徴 ・物流ロボットに関連する情報システム ・物流ロボットの普及[…]
ACRとは?
ACRの定義
ACRとは、Autonomous Case-handling Robotの略称です。日本語で言うと、自律走行してケースを扱う(=ケースハンドリングする)ロボット、というようになるかと思います。
ケースは、物流でよく言うケースかバラか、のケースです。箱、段ボールとも同義です。ケース状の物ということで、ケースそのものや、中にバラ品を収納したコンテナを扱います。つまり物流でハンドリングする荷姿そのもの、もしくはその一歩手前の状態とも言えます。このケースおよびコンテナ(以降、ケース/コンテナと記載します)をダイレクトに運搬して、保管用のラックに出し入れするロボットがACRです。
ACRの構成要素
ACRの基本的な構成要素は次の通りです。
- ケース/コンテナを保管するための高層ラック
- 高層ラックからケース/コンテナを出し入れして、複数個をまとめて運搬するロボット(ACR)
- ロボット(ACR)と人(作業者)の間でケース/コンテナを受け渡しするための作業ステーション
入荷の時はコンテナが作業者→ロボット→高層ラックと受け渡されて行きます。出荷の時はその逆です。
ACRを活用するメリット
出荷に伴う作業者の歩行が無くなる、GTP(Goods To Person)方式のソリューションで高い生産性を実現します。詳しくは後述しますが、GTPの先駆けであった棚搬送AGVは棚を丸ごと運搬するのに対して、ACRは出荷等の作業の対象になるケース/コンテナのみをピックアップして運搬するため、(常にというわけではありませんが多くの場合に)より効率的な仕組みと言えそうです。よりきめ細かなGTP、Detailed GTPのような言葉があってもいいのかもしれません。
ACRを活用した場合の生産性は、一般的な、作業員によるピッキング(作業員が荷物を保管したロケーションまで歩いて行ってピッキングする方式)と比較して、2~4倍程度は高くなるとされています。
ACRには、生産性に加えて、保管効率を向上させるメリットもあります。高さ5メートルくらいの高層ラック(※)を使って荷物の収納量を増やすことにより、その保管効率は、一般的な高さ2メートル程度のラックを使う場合と比較して、1.5~2倍程度になるとされています。
※建築物の要件が許せば、高さ10mのラックにも対応可能。
ACRと他の物流ロボットの共通点および違い
まず、以前の記事で整理した物流ロボット(荷物の保管~出荷に活用されるロボット群を指して「ピッキング用搬送ロボット」としています)のタイプをここで再掲します。
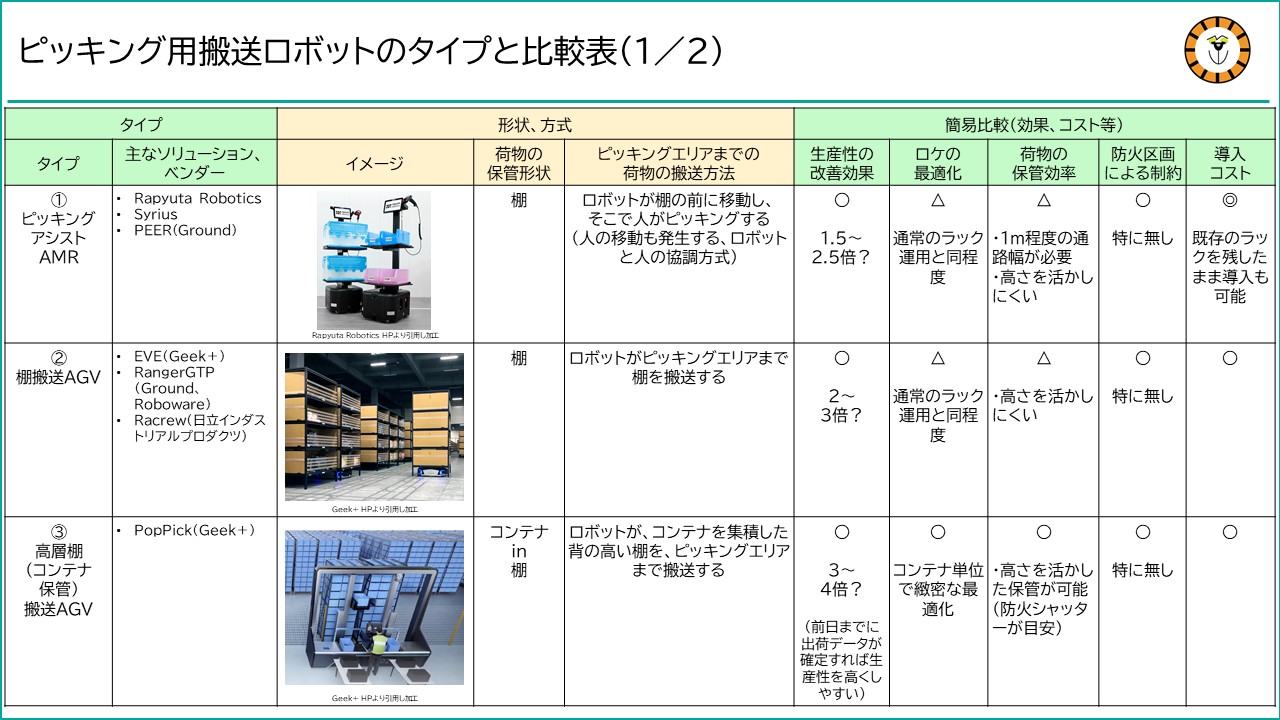
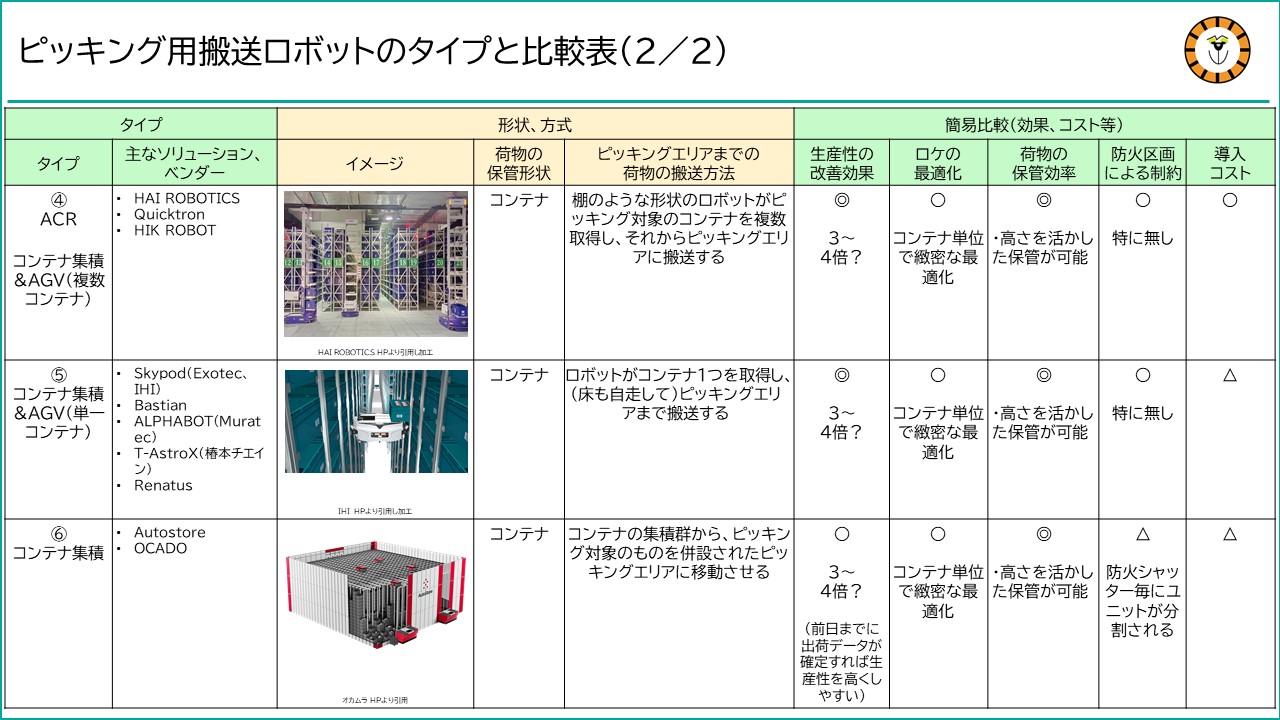
ここではACRをタイプ④としています。
まず全体を概観しますと、タイプ①のピッキングアシストAMRは人の移動を削減する半自動の方式。そして、タイプ②の棚搬送AGVがいわゆるGTP(Goods To Person)方式の先駆けでした。タイプ②に対して、ACRを含むタイプ③~⑥は、より高さを活かして保管効率を向上するという特徴を付け加えたようなイメージです。
タイプ③~⑥について、GTPと、高さを活かした保管効率の2つは大きな共通点ではあるものの、比較表にある通りそれぞれ形状や運用方式、また導入コストなども異なります。どれが優れているか、そうでないかと一概に言えるものでもなく、取り扱う荷物の種類や業務の内容に応じて、どれがよりフィットするかを慎重に検証する必要があります。実際、これらのソリューションは頻繁に比較・検討されているようです。(この後のパートで、タイプ④ACRとタイプ②棚搬送AGVとの簡単な比較を行いますので、よろしければ参考にされてください。)
ただし、今回取り上げているACRをはじめ、高さを活かすタイプが目立って増えてきており、このことは、土地が限られていて保管コストが高くなりやすい日本では、特にハマるトレンドなのではないかと考えられます。さらにACRは、後で詳しく説明しますが、多品種で、出荷頻度がそれほどは高くはない、小ロットのアイテムで特に高いパフォーマンスを発揮します。日本ならではのきめ細かな物流サービスを支えてくれるソリューションとも言えそうです👍
他の高層タイプのロボットと比較して、導入コストが小さく抑えられそうな点も期待が高いです。
この比較表と各ロボットの紹介を含む記事はこちら
[最新の更新内容]ソリューションの比較表を更新しました。 -------------------------------------------------------------- 前回の記事では物流ロボットの内、入荷(デバン[…]
ACRを含め、高層化したロボット(比較表におけるタイプ③~⑥)が増えているというトレンドを詳しく解説した記事はこちら
トラロジが特に注力しているテーマのひとつである物流ロボットについて、今回はここ数年で特に顕著になっている2つのトレンドをわかりやすく整理してお伝えしたいと思います。 トレンドのひとつは、物流ロボットが高層化し、また高密度に荷物を保管するこ[…]
ACRと自動倉庫の違い
自動倉庫(AS/RS:Automated Storage and Retrieval System)との違いにも触れておきます。自動倉庫は従来からある業務自動化のソリューションですが、非常に大掛かりな設備であり、大きな投資を必要とします。そのためかなり限られたケースでしか活用できないものと思われます。また、固定的な設備であり、業務量の増減に対する柔軟性や拡張性があまりありません。自動倉庫一式の設備を丸ごと増やすか、減らすか、というとても大掛かりな対応になってしまいます。また、単体としての能力は高いものの、特定のレーン(エリア)に出荷が集中してしまった場合などには全体としての能力が落ちてしまう可能性があり、それを補う能力増強をすることもできません。
ACRは相対的にコンパクトで柔軟な設備になります。導入コストも抑えられるため、自動化・省力化の裾野を広げるソリューションと言えます。具体的には、自動倉庫と以下のような違いがあります。
- 建物の躯体を工事する必要がない。
- 防火区画を跨いだ設置が可能。
- 短納期で設置が完了する。
- 他倉庫への移設も可能。
- 電力容量が小さい。
ACRで何ができるのか? どんな場合に向いているのか?
ここではACRの特徴を踏まえて、ACRで何ができるのか、特にどんな場合に高いパフォーマンスを発揮しやすいかを考察します。ただし、ACRは、要は「ケースやコンテナサイズの荷物を効率的に扱う仕組み」ですので、ここで紹介する以外にも、発想次第では様々な活用可能性がありうると思われます。ですので、ここからの内容は、あくまでも代表的な活用方法ということでご確認ください。
説明がやや長くなりそうですので先に簡潔にまとめますと、次のようになります。
- ACRで扱うことができる荷物のサイズは、ケースそのものか、オリコンに収納できるバラ品。混在もOK
- ACRは多品種、(出荷頻度が)中頻度、(出荷量が)小ロットのアイテムに特にフィットするソリューション
- ただし、そういったアイテムに限定することが必ずしも正解とは言えない。その他のアイテムも統合的にACRで管理することで、トータルに生産性を向上させられる可能性もある
ACRで扱う荷物のサイズはケース、オリコンまで
まずは、形状からして当たり前のことなのですが、ACRはケース、オリコンのサイズまでの荷物を扱うのに向きます。オリコンで言うと70リットル程度のサイズが一般的と思われます。荷物のサイズが、このサイズそのもの、要はケース単位で扱う場合か、このサイズのコンテナにバラ品とし収納できる場合に、ACRを活用することができます。ACRで、ケース単位の業務(例えば店舗向けの出荷)とバラ品の業務(例えば通販の個人客への出荷)を同時に混在して扱うことも可能です。
ケースとオリコンのサイズのバラツキには、対応できるACRとそうでないものがあります。ケース、オリコンを高層ラックから一つずつ取り出して、まとめて移動させるのが、ACRの特徴であり制約でもあると言えます。
SKUあたりの出荷量が少ない、「小ロット」のアイテムに最適
ACRによる生産性向上のメリットが特に大きくなりやすいのは、SKUあたりの出荷量がそれほど多くないアイテムです。少数のケースを出荷する場合や、バラ品の出荷数がコンテナ1つに収納できる範囲の場合です。
逆にSKUあたりの出荷量が多いと、ACRがケース、コンテナを出し入れする回数、それを移動させる回数が増えて、時間が掛かってしまいます。ですので、出荷量がかなり多いアイテムについては、ACRの外で管理して、作業員が歩いて移動し、台車やパレット等を使って一度に大量にピッキングする方が、生産性が高くなる可能性があります。ACRでケース、コンテナを沢山出し入れしながらピッキングするのと、作業員が歩いてもしくはフォークリフトを使って移動して一気にピッキングするのと、どちらが早いかでACRを使うべきかどうかが分かれます。
出荷頻度が「中頻度」くらいのアイテムに最適
出荷頻度は、中頻度程度がもっともACRのパフォーマンスを発揮しやすくなると考えられます。
出荷頻度がかなり高いアイテムの場合は、あらかじめ限られたスペースに集めて作業員の移動を限定してしまい、作業員が集中的にピッキングする方が、生産性が高くなりやすいと考えられます。高頻度のアイテムを集約したエリアを設けて、DPS(デジタル・ピッキング・システム)を活用してピッキングの生産性を上げる、といった方式がよく見られます。
出荷頻度が中程度であれば、ACRを活用することで歩行レスになり生産性が向上するメリット、また保管効率が向上するメリットを大きく享受することが期待されます。
なお、出荷頻度がかなり低い場合には、その保管場所としてACRを活用することがコスト面で見合わない可能性も出てきます。ACRを活用して保管するコストと、ACRの外で管理して出荷する際にかかる作業コストのどちらが大きいかで判断することになります。
「多品種」のアイテムを扱うのに最適
アイテムは多品種の方がACRの活用に向くと考えられます。ここまでの説明でACRがそのパフォーマンスを発揮しやすいとした、中頻度で小ロットのアイテムは、多品種を扱うほど増えてくるものです。また、ロボットに関連する投資額も小さくはないため、多品種を扱う、相応の規模の物流センターであればそれだけ投資対効果が見合いやすくなる、という点もあります。
「最適」以外の領域にも広げて活用するメリットがある
ここまで、ACRは多品種、中頻度、小ロットのアイテムに最適と説明してきました。では、それ以外の領域では、ACRは使わない方がよいのでしょうか?🤔
ある特定の限られたアイテムについて、ACRの外で作業をする方がそれ単体での効率がよいことはもちろんあります。ただし、他の多くのアイテムをACRで取り扱う場合には、ACRの適用範囲にまとめてしてしまった方が、業務プロセスが統一されて作業が簡単になり、情報も統合されて、シンプルでわかりやすい運用になって、結局は生産性が高くなる可能性も高いと思われます。そのためACRの活用範囲は、ここで最適としている領域そのものよりも広くなることが多いのではないでしょうか。
ACRと棚搬送AGVの向き・不向きを比較
ここでACRと、KIVA(Amazon)やEVE(Geek+)、RangerGTP(Grey Orange)のような棚搬送AGVとを比較するのもわかりやすいと思います。
図表で示すとわかりやすいのでこちらをご覧ください。
繰り返しになりますがACRは多品種、中頻度、小ロットのアイテムに最適で、非常に高い生産性を実現することができます。
棚搬送AGVの場合は、小ロット品ですと、棚全体を移動させる方式のため関係のないアイテムまで動かしてしまう可能性があり、相対的に効率が下がりやすくなります(その棚に含まれる複数のアイテムが同時に出荷される、いわゆるヒット率が高い場合はその限りではないですが。ヒット率が高い方がよい、となると、出荷頻度もある程度高いアイテムが向くと考えられます。)
逆に大ロット品においては、相対的に棚搬送AGVの適性が高くなります。ピッキング間口を(ACRではコンテナ1つなのに対して)最大で棚1台分まで割り当てることができるため、より大きな出荷ロットまで対応しやすくなるためです。また、同じく間口が大きいという理由で、単純にACRよりもサイズの大きなアイテムにも対応することができます。
それぞれ適性の異なるロボットなので、アイテムの特性に応じて上手く使い分けしなければなりませんね。
ACRの主要なソリューションを紹介
ACRの主要なソリューション、メーカーを紹介します。いずれも中国発のロボットメーカーになっています。
中国はEC(Eコマース)の普及率(EC化率=小売に占めるECの割合)が世界の中でも圧倒的に高く、40%を超えるとされています。日本のEC化率は、年々上昇してはいますがまだ10%前後で、中国の4分の1くらいです。そして、世界全体のEC市場に占める割合は、中国が約50%、日本は約3%です😵。小口のアイテムをそれだけ大きなボリュームで扱う中国で、自動化・省力化の優れたソリューションが生まれるというのは、必然なのかもしれません。日本でも、EC化率はおそらくもっと高くなっていきますし、何より人手不足の深刻さが増していきますので、ACRやその他の自動化・省力化ソリューションを積極的に活用していくことは不可欠だと思います。
HAI ROBOTICS JAPAN
HAI ROBOTICSは2016年に設立された、中国発のロボティクスソリューション企業です。2021年に日本法人であるHAI ROBOTICS JAPANを設立しました。
今回取り上げているACRという、ケース、コンテナを取り扱うロボットのパイオニアとされています。2023年2月時点で、グローバルでACR導入プロジェクト数が累計500以上、ロボットの販売台数が5,000台以上とされており、パイオニアであり現時点のリーダー企業と言えるでしょう。
関連する特許も1,100を超えており、知財の面でも高い競争力を持っています。
- HAI ROBOTICSのホームページ
- HAI ROBOTICSの関連動画
この特集の後、ACRのリーダー企業であるHAI ROBOTICS社にインタビューを行わせていただきました。同社ソリューションの特徴や強みを掘り下げて聞いています。インタビュー記事はこちら
この記事の公開日は2023/5/26です。 ------------------------------- 物流ロボットの一種である、ケースハンドリングロボット(ケースやオリコン単位での荷物の取り扱いを自動化するロボット)の「A[…]
HIK ROBOT
HIK ROBOT(ハイクロボット)も中国発のロボットメーカーです。ACRの他に棚搬送ロボット、重量物の搬送ロボット、自動フォークリフトなど様々なソリューションを提供しています。
HIK ROBOTではACRとは呼称しておらず、CTU、Carton Transfer Unit、カートン(箱)を移動させる仕組み、としています。考え方や構造はACRと基本的に同じです。
- HIK ROBOTのホームページ
- HIK ROBOTの関連動画
Quicktron
Quicktronは2014年に設立された中国発のロボットメーカーです。2020年に日本法人も設立されています。「QuickBin(クイックビン)」シリーズというACRを提供しています。QuickBinの大きな特徴は、ロボットが2種類に分かれている点です。高層ラックからケース/コンテナを取得する背の高いロボット(親機)と、親機からケース/コンテナを一つずつ受け取って搬送するロボット(子機)、という役割分担にすることでより効率的な運用が志向されています。一方で、ロボット台数が増える分、導入費用は大きくなりそうに思います🤔
QuicktronはACRの他に棚搬送AGVや自動フォークリフトなども提供しています。
- Quicktronのホームページ
- Quicktronの関連動画
ギークプラス
ギークプラスは2015年に中国で創業し、2017年には日本法人が設立されました。棚搬送ロボットのEVEシリーズが2018年~2020年の3年連続で国内シェア1位とされており、GTP方式の普及をリードする企業です。
ACRに相当する製品として「RoboShuttle」を、日本では2025年から提供しています。Quicktronと同様に、高層ラックからケース/コンテナを取得する親機(ACR)と、親機からケース/コンテナを受け取って搬送する子機(AMR)とに分かれる構成です。ギークプラスは元々他に、高層のラックを移動させる、棚搬送ロボットの背が高いバージョンともいうべきPopPickというソリューションを展開していました。そこに新しくRoboShuttleが加えられています。
- RoboShuttleの製品紹介ページ
- RoboShuttleの関連動画
ACRの導入事例、活用シーン
最後に、実際にACRを活用している事例について簡単に紹介します。もっと細かい、事例の具体的な中身については、ここでは長くなり過ぎてしまうため、また別の機会を作って詳しく紹介できればと思います。
ACRが活用されている業種/業務
まずACRが活用されているアイテムの種類としては、アパレル、家電、精密機器、電子部品、自動車部品(タイヤ)、医薬品、日用品、書籍などなど・・・幅広い種類があります。ACRが特に高いパフォーマンスを発揮しやすい条件として先に説明しました、多品種、中頻度、小ロットに当てはまるアイテムであれば、広く対応することができるということですね。例えばアパレルは、一般的にアイテム種類が多く、売れ筋もコロコロ変わるため、こういった条件に当てはまることが多そう、というのは想像しやすいかと思います。
適用される業務領域としては次のようなものがあります。
- 物流倉庫から小売店舗への出荷
- 物流倉庫から一般顧客へのEC出荷
- 物流倉庫で受領する返品商品の管理
- 工場内物流
アパレルを例に、ACRの活用シーンを紹介
ACRが実際にどのように活用されているか、動いているのかをイメージしていただけるように、導入事例を一つ紹介したいと思います。アパレルを例にとります。
先に挙げたACRのソリューション各社の中でも、特にHAI ROBOTICSが既に多くの導入事例を公開してくれていて、活用方法や流れもわかりやすいので、そこから一つピックアップします。
この中から、ANTAの事例を紹介します。ANTAは中国の大手スポーツアパレル企業で、日本でもよく知られているブランドとしてはFILAやDESCENTがANTAのグループに含まれています。ANTAではこれまでに合計600台以上のACRが導入されており、まさにその物流を支える基幹ソリューションという位置付けになっています。
詳しくはANTAの事例動画を見ていただければよいのですが、ここではハイライトとして切り取った内容も掲載します。
https://www.hairobotics.com/jp/cases/anta-group-chengdu
最初に、ACRを導入した倉庫の概観から。高層で高密度な保管になっていることがよくわかります👍
入荷の流れを見ていきます。作業者が行うのは、入荷したアイテムと格納するコンテナとの紐づけのみです。コンテナをコンベヤラインに載せると、あとは自動でACRに積み込み、ACRが格納先のロケーションまで搬送して格納(入庫)します。
続いて出荷の流れです。入荷と逆の流れで、ACRが出荷対象アイテムを格納したコンテナを取得し、コンベヤラインに移してピッキングエリアに届けます。作業者は画面に指示された数量のアイテムをコンテナからピッキングして、この事例ではそれを出荷用のコンテナに格納します。出荷用のコンテナも表示器で指定されるため非常に簡単な作業になっています。
入荷、出荷ともに、とてもシンプルな作業になっていることがよくわかります。作業者が保管エリアに入る必要がなく、歩行時間が発生しません。複雑な作業が無く、保管ロケーションを把握する必要もないため、短時間で作業を覚えて生産性を発揮することができそうです。
QuickTronのQuickBinについても、Youtubeでは数件の導入事例が紹介されています。これはLi & Fungという企業で活用されている事例です。
今回の記事で紹介した通り、ACRは無駄のない、よりきめ細かなGTP方式によって生産性を高めることができ、また保管効率も高くなるため、日本の環境に向く、理に適ったソリューションではないかと期待しています。日本での本格展開もまさにこれからなので、ここ数年で活用が広がっていくのではないでしょうか。
今後もACRに注目し、有力なソリューションやその導入事例を取り上げていきたいと思っています。お楽しみにお待ちください!