This is the second part of the featured article on Rapyuta Robotics, the domestic market share leader (for three consecutive years from 2020 to 2022) in the picking assist AMR, which is increasingly being introduced as a logistics robot.
In the first part, we focused on the technical and functional strengths of Rapyuta Robotics’ picking assist AMR.
we interview Rapyuta Robotics, which has the largest market …
In this second part, we would like to address the implementation program that the company offers to ensure the effectiveness of this solution, which is superior in terms of technology and functionality, as well as the level of customer success.
- 1 Providing a reliable program that guarantees cost-effectiveness and lowers the hurdles to AMR implementation.
- 2 Thorough customer success to ensure clients’ success.
- 3 Customer feedback obtained through customer success program accelerates the development of solutions
- 4 Future prospects of Rapyuta Robotics.
- 5 Editor’s Note
Promotional video of “PA-AMR” by Rapyuta Robotics
Continuing from the first part, we interviewed Mr. Ryo Mori, Executive Officer and Business Supervisor of Rapyuta Robotics.
Providing a reliable program that guarantees cost-effectiveness and lowers the hurdles to AMR implementation.
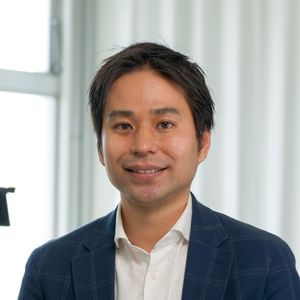
The first is the provision of an implementation program aimed at reducing the uncertainty or risk associated with AMR adoption. In June 2022, we began offering a “cost-effectiveness guarantee program” for subscription-based AMR usage. Most customers will be introducing AMR for the first time, with high expectations for productivity gains but also with considerable concerns about whether they will be realized. The aim of the program is to alleviate these concerns. Before introducing AMR, we conduct detailed simulations of the implementation plan and expected outcomes, and set a target productivity level. If this target is not achieved after implementation, the subscription fee for the AMR will be reduced accordingly. Therefore, customers can start using AMR with peace of mind, as long as they are satisfied with the targeted productivity level.

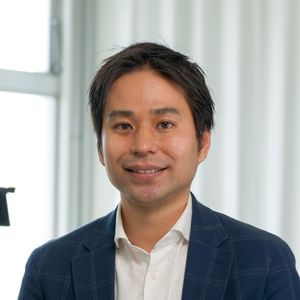
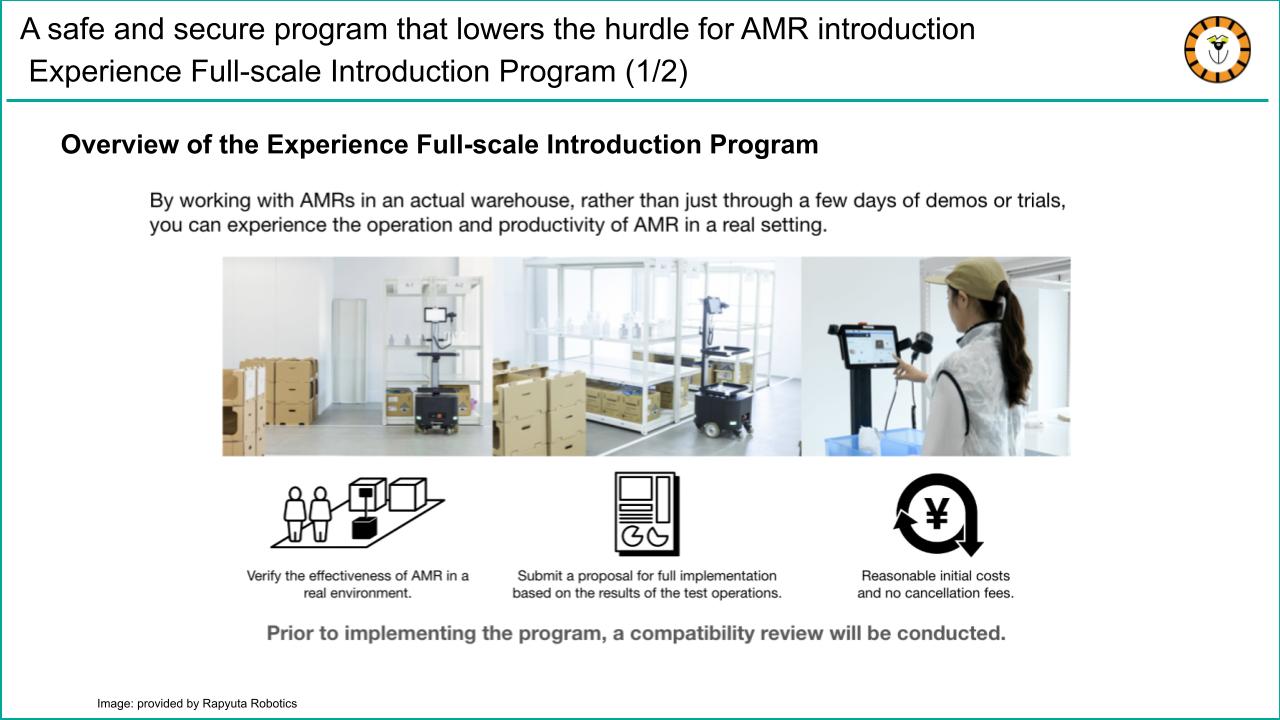
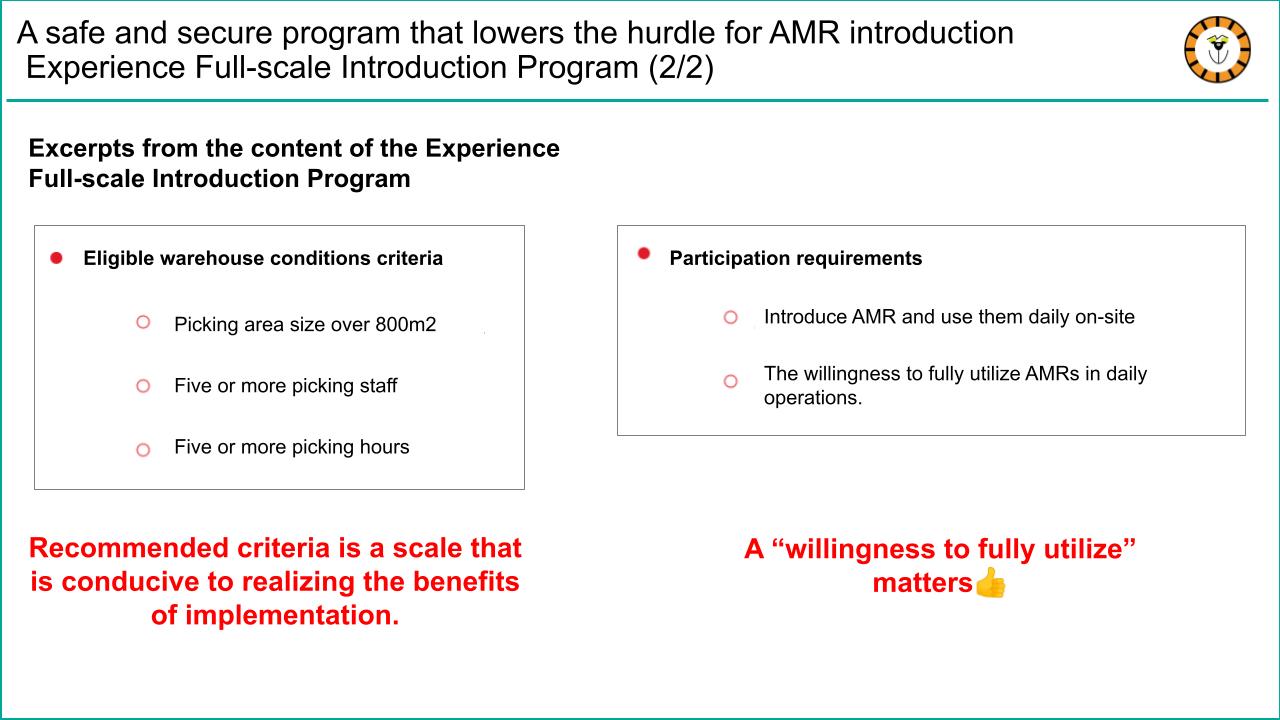
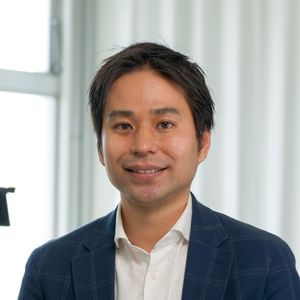
Thorough customer success to ensure clients’ success.
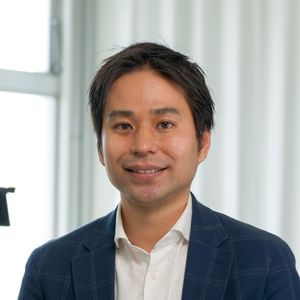
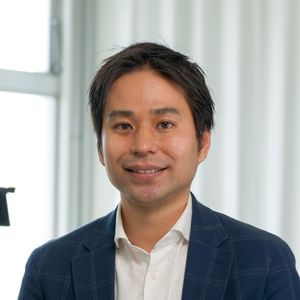
Once every quarter, we hold a large-scale review meeting with our customers to summarize the quarter, share future goals and activity plans.
During these communications, we always adhere to a style of proactively proposing improvements. Instead of passively receiving challenges from customers, we extract their challenges and encourage necessary changes from both sides. To maintain this style, we require not only the technical ability to continuously improve the content of our solution but also a deep understanding of logistics operations that is on par with our customers. Our Customer Success team has members who are knowledgeable about logistics operations, and we propose the best ways to use AMR after understanding the customer’s business processes.
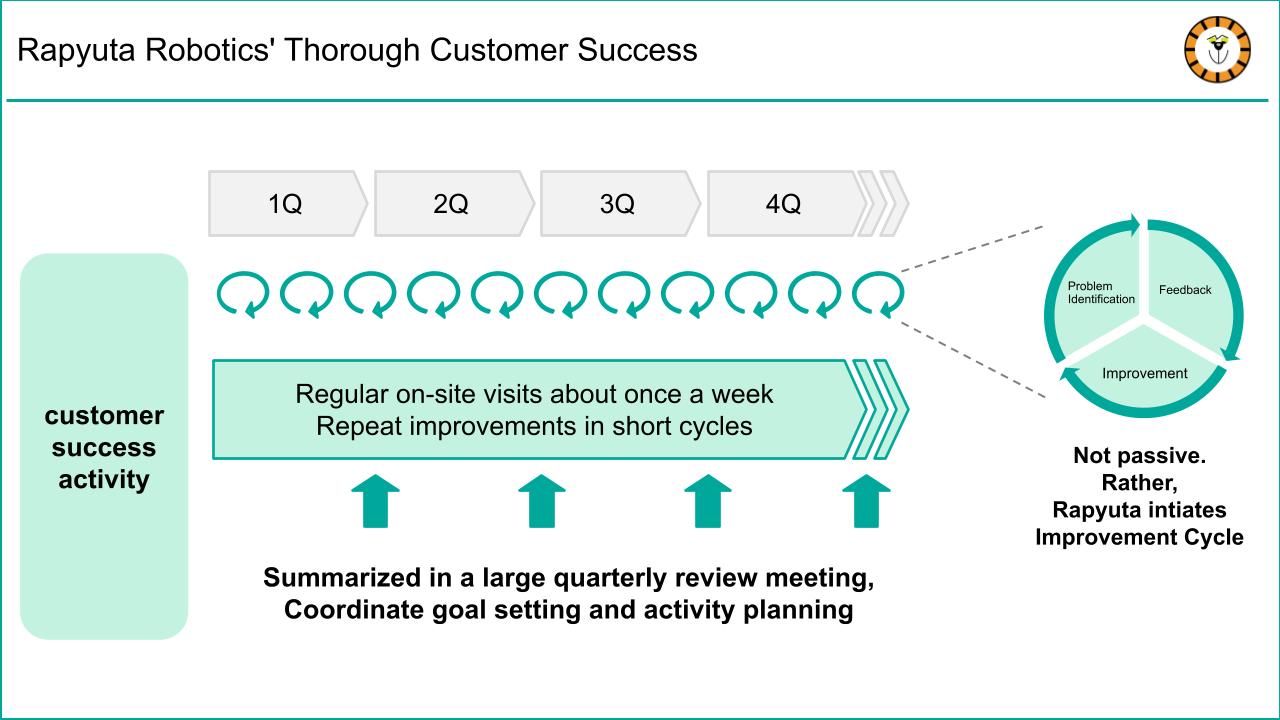
Customer feedback obtained through customer success program accelerates the development of solutions
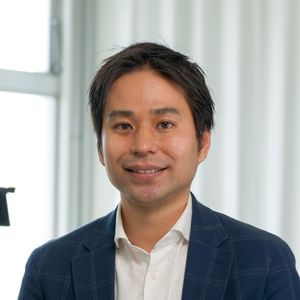
Since we focus on customer success, we receive a lot of feedback from our customers. From this feedback, we prioritize incorporating features and services that benefit everyone, not just specific customers. For example, the Picker Guidance System, which suggests the next picking location for the AMR, was born from customer feedback. We also added support for loading cardboard in addition to foldable containers, and implemented a fire shutter integration that automatically moves the AMR to a safe location when a fire alarm is triggered. We also have a productivity tracking feature that displays the productivity of individual workers on a dashboard.
By providing attentive support for individual customer needs, we are able to evolve our solutions. This creates a positive cycle where we can provide higher quality solutions to all of our customers.
Future prospects of Rapyuta Robotics.
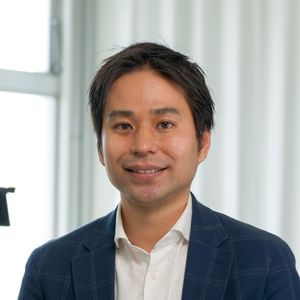
At Rapyuta Robotics, we aim not only to provide robot solutions, but also to provide a platform (something like a brain that effectively moves multiple robots) for more effective and efficient use of robots. As our own lineup of robots expands, they will be able to smoothly collaborate with each other, and the types of tasks and items that they can handle will also expand. In addition, we will be able to support other companies’ robots and material handlers, and integrate them into the same platform, or “brain”, to easily create highly productive workflow processes. This will bring us closer to a state where all robots and material handlers are optimally coordinated using the same platform, creating highly productive workflow processes.
Editor’s Note
I am very grateful to Mr. Mori of Rapyuta Robotics for taking time out of his busy schedule to talk to us in depth about AMR. It goes without saying that their AMR technology is an excellent solution, but I also feel their strength as an organization in how they fit it into business through customer success and adoption programs with performance-based incentives. I have also talked with other members of Rapyuta Robotics, and while they all seem to be highly skilled and sharp, they also have a commitment to achieving results that I find admirable.
As for the vision of various robots and material handlers collaborating easily and efficiently, it is an ever-growing market, and I am excited to see how Rapyuta Robotics will expand within it.
Their expansion to the US is also fascinating. (I don’t know much about the logistics industry in the US, to be honest 😑, but) the solutions developed in Japan, with its meticulousness, may have an even greater impact in the US. Given that labor costs are higher in the US, the effects could be significant in that regard. I hope they will also thrive in the US.